Steelmakers, mostly in China and India are, in fact, increasing toxic coal-run blast furnace capacity instead of switching to greener technology, says report
Global steelmakers are nowhere on the path of decarbonisation. In fact, they are building more coal-run blast furnace (BF) based capacity compared to electric arc furnaces (EAF) which are comparatively cleaner and greener, says the new annual Global Energy Monitor report.
The report warns that this could risk around $518 billion in stranded asset as countries struggle to meet their long-term carbon neutrality commitments, if the 345.3 million tonnes per annum (mtpa) of emissions-heavy blast furnace basic oxygen furnace capacity (BF-BOF) proposed or under construction is fully developed.
The global steel and iron industry is off track from IEA’s net zero pathway that requires the share of electric furnaces capacity to increase from 31% where it is now to about 37% by 2030 and 53% by 2050.
China and India represent 80% of new dirty Blast Furnace capacity
India has the second-most polluting steel sector in the world, preceded by China, says the report. Much of this stranded asset risk is concentrated in Asia. Around 80% of the BOF steelmaking capacity under development globally is planned in China (158 mtpa with up to $237 billion) and India (123 mtpa; up to $184 billion). An additional 14% of the BF-BOF steelmaking capacity under development is planned for Indonesia (24 mtpa, $35 billion), Vietnam (16 mtpa, $23 billion), and Malaysia (12 mtpa, $17 billion).
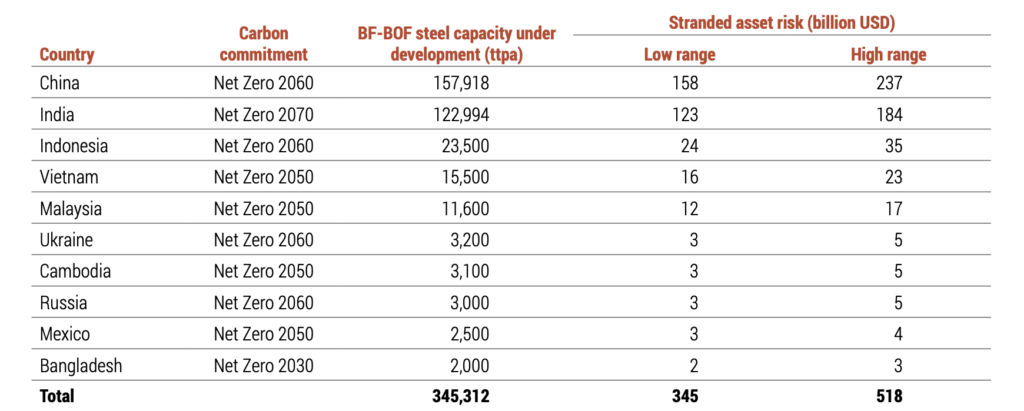
Good start: Can countries at least shut down units running overcapacity ?
The report also highlights data on how much countries are running overcapacity in steel production. India has a steel overcapacity of 14%, while the US and Germany have 30% and 25% respectively. Can countries therefore shut dirty BF-BOF units producing surplus without harming annual production?
For example, Germany has a steel overcapacity of 25%. This means looking at current country-wise steel production capacity numbers—Germany has a total steel capacity of 48.060 ttpa (thousand tonnes per annum), 25% of this would amount to a 12,015 ttpa or 12 Mtpa overcapacity. The report says that Germany could close higher-emitting BF-based steel capacity or switch to cleaner production technology without impacting its yearly production.
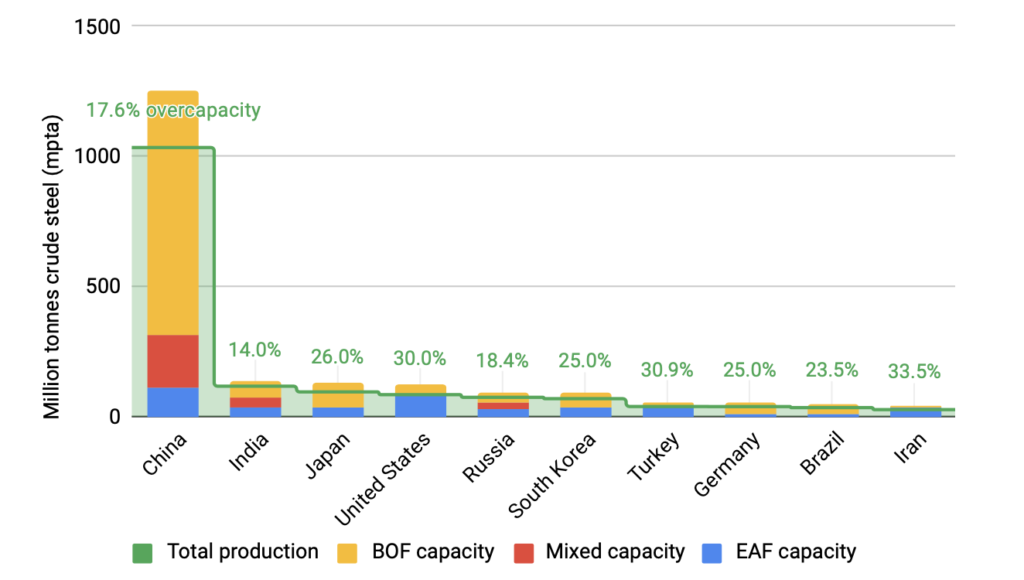
Policies lack clear standards, definitions?
The report states that transition from BF-BOF technology to EAF technology will be driven by market demand, policy interventions, and producer incentives for lower emissions steel. What’s required is a push towards green steel demand, policies and incentives for lower emissions steel production, clear emissions-based definitions of low-emissions versus near-zero emissions are critical.
Steelmaking: Underreported emissions point to coal
Emissions from steelmaking are much greater than reported when coal mine methane emissions are considered, the report states. The steel industry currently emits approximately 2.6 Gt direct CO2 emissions and 1.1 Gt indirect CO2 emissions from the power sector and combustion of steel off-gases. Methane emissions from metallurgical coal mining could add an additional 1 Gt CO2-e20 to this footprint, a 27% increase.
Steelmaking emissions around 27% higher than currently reported
The steel industry only calculates direct and indirect emissions, which typically include the process emissions of the chemical reaction and operation of iron and steel units (direct emissions), and emissions of energy generated to operate the steel plant (indirect). Other emissions include raw material transport and post-production processing. However, the report points out that steel industry emissions assessments do not account for coal mine methane. Steel production can consume both types of coal, thermal and metallurgical coal. Thermal coal is consumed when a steel plant uses coal-based power, but it is challenging to assess without better data on power sources for each steel plant, the report states.
Metallurgical coal is consumed by the steel industry in the BF-BOF production process that uses approximately 770 kg of metallurgical coal per tonne of steel. The global thermal coal operations (intended for power generation) emit 28 million tonnes of methane, a number identical to the IEA’s findings in its latest Methane Tracker (2022). and global metallurgical coal operations currently emit 9.4 million tonnes of methane per year, with mixed thermal and metallurgical coal mines emitting an additional 5 million tonnes of methane.
As per the IPCC’s methane global warming potential standards, the world’s operating metallurgical coal operations currently emit 280- to 780 Mt CO2-equivalent emissions each year (when averaged over 100 and 20 years, respectively). Mixed thermal and metallurgical coal mines emit an additional 150 to 410 Mt CO2-equivalent emissions per year. The steel industry currently emits approximately 2.6 Gt of direct CO2 emissions per year and 1.1 Gt of indirect CO2 emissions from the power sector and combustion of steel off-gases. If the methane emissions from metallurgical coal mining are accounted for in global assessments of steelmaking emissions, the footprint of the steel industry may be as much as 27% (1 Gt CO2-e20) higher than currently reported.
The report raises concerns about unaccounted emissions in steel decarbonisation plans that rely heavily on retrofitting coal-based steelmaking with carbon capture, utilisation, and storage, rather than fully abandoning this technology.
About The Author
You may also like
Why AC Limits Aren’t Enough in Heat-Stressed India
Closing the SDG Gap: Why Financing for Development Must Scale Now
Nearly 3,000 Climate Lawsuits Filed Since 1986: Report
Climate Talks in 2025: Converging Crises, Rising Stakes, and Diminished Returns
MCL to invest ₹40,000 crore to set up 4GW thermal power plant